Smart manufacturers are always looking for ways to decrease operating expenses, increase overall efficiency, reduce downtime, and maximize production.
To this end, more and more manufacturers are investing in intelligent manufacturing technology that enables them to create highly adaptive, efficient, and responsive production systems that enhance output and improve product quality while minimizing waste.
Due to the myriad benefits the technology provides, it comes as no surprise that the global intelligent manufacturing market is projected to bring in $754.1 billion by 2030, an uptick from $310.92 billion it brought in during 2023, according to Fortune Business Insights.
Keep reading to learn more about intelligent manufacturing, its benefits and challenges, intelligent manufacturing use cases, and some key technologies that enable it.
Table Of Contents
What are the benefits of intelligent manufacturing?
The market for smart manufacturing is growing rapidly thanks to the transformative benefits the new approach to production delivers.
Increased efficiency
Leveraging advanced technologies like automation, IoT, AI, and edge computing, intelligent manufacturing streamlines production processes and eliminates inefficiencies, leading to a more profitable operation. Using real-time streaming data and analytics, manufacturers can optimize workflows in the moment, reducing bottlenecks and minimizing downtime.
On top of this, intelligent manufacturing enables organizations to automate repetitive tasks, ensuring consistency and speed while reducing errors and freeing up staff to focus on more complex tasks. As a result, production cycles are faster, throughput is higher, and overall operational efficiency is significantly improved, enabling manufacturers to meet demand effectively while accelerating time-to-market.
Improved product quality
By integrating real-time monitoring and advanced analytics, smart manufacturing improves product quality by enabling companies to detect defects earlier in the production process. AI-driven quality control systems continuously analyze data from production lines to identify variations and anomalies as soon as they emerge. Using predictive analytics, manufacturers can anticipate potential quality issues before they occur, allowing for proactive adjustments.
Taken together, intelligent manufacturing leads to more consistent production standards, better quality products, less rework, increased customer satisfaction and, ultimately, a healthier bottom line.
Reduced costs
Intelligent manufacturing reduces costs by optimizing resource allocation, minimizing waste, and managing energy efficiently. At the same time, automation reduces labor costs by handling time-consuming repetitive tasks. On top of this, predictive maintenance reduces the frequency of unplanned downtime, keeping lines of production running at peak capacity longer with lower maintenance costs.
Today’s leading smart manufacturing shops are laser-focused on continuous improvement, using advanced analytics to identify areas for cost-savings — like optimizing the supply chain or improving inventory management. By cutting down on waste, decreasing energy consumption, and improving overall operational efficiency, intelligent manufacturing helps manufacturers reduce costs substantially.
Enhanced decision-making
By embracing intelligent manufacturing, organizations improve decision-making through the use of real-time data and advanced analytics. By collecting data across every stage of production and analyzing it in real time, manufacturers can extract the actionable insights they need to streamline production. This data-driven approach enables managers to make better-informed decisions about production planning, resource allocation, and process improvements, among other things.
Thanks to predictive analytics, intelligent manufacturers can forecast future trends, identify potential issues, and make proactive decisions to keep operations humming along. By leveraging accurate, up-to-date information, manufacturers can make strategic decisions that enhance productivity, quality, and overall operational performance — and enjoy better business outcomes because of it.
What are the challenges of intelligent manufacturing?
To take advantage of those benefits, intelligent manufacturers first need to solve for several profound challenges.
High implementation costs
Implementing intelligent manufacturing systems involves significant investment in several technologies, including automation, IoT, AI, edge computing, and real-time data platforms. In addition to hardware and software expenses, costs also include the infrastructure needed to support these systems — like sensors, IoT devices, upgraded network capabilities, and robust cybersecurity measures.
Additionally, manufacturers also need to account for ongoing maintenance, upgrades, and employee training, which can be a financial burden. For many manufacturers — and smaller shops in particular — these high costs can be a significant barrier to adopting intelligent manufacturing solutions.
Real-time data management and analytics capabilities
Managing and analyzing the vast amounts of real-time data intelligent manufacturing systems require is only possible when you have the right data infrastructure in place. This entails high-speed networks, real-time data platforms, scalable storage solutions, edge computing infrastructure, IoT devices, and advanced data processing capabilities.
To make the most of intelligent manufacturing, organizations need to be able to move at the actual speed of real time — in less than 10 milliseconds — positioned to rapidly respond to new information as soon as it’s known.
Skills gaps
In addition to technology, manufacturers also need a workforce skilled in advanced technologies like AI, IoT, and real-time data processing. Unfortunately, since these technologies are all relatively nascent, there’s often a skills gap that employers struggle to fill as applicants and existing staff lack the expertise required to maintain sophisticated systems.
To address this skills gap, organizations should implement comprehensive training programs and potentially hire new talent with the requisite skills if they can find it. Both of these tactics can take a lot of time and require a lot of resources, which can pose a barrier to rapid intelligent manufacturing adoption.
Integration with existing systems
Of course, intelligent manufacturing technologies also need to play nicely with legacy systems — something that’s often easier said than done.
Such systems can be outdated, lack interoperability, or have limited data integration capabilities, making the integration process a nightmare. Even in the best circumstances, integration with legacy systems often requires significant modifications, custom interfaces, and extensive testing to ensure compatibility and minimize disruptions.
Additionally, managing the transition to new technologies while maintaining ongoing production can be challenging. As such, effective integration requires careful planning, a phased implementation approach, and hand-in-glove collaboration between IT and operations teams to achieve a cohesive and functional intelligent manufacturing ecosystem.
Intelligent manufacturing use cases
How exactly are organizations using smart manufacturing to achieve better business outcomes? Let’s take a look.
Predictive maintenance
Using IoT sensors and advanced analytics, intelligent manufacturers can use predictive maintenance to monitor equipment health, predicting and fixing failures before they occur. By analyzing real-time data on machine performance and conditions, manufacturers can schedule maintenance activities proactively, reducing unplanned downtime and extending equipment lifespans.
This approach minimizes repair costs, enhances operational efficiency, and ensures continuous production by nipping potential issues in the bud before they metastasize.
Supply chain optimization
Intelligent manufacturing leverages AI and data analytics to optimize supply chain operations, enhancing visibility and coordination across the entire supply chain. By integrating and analyzing data from suppliers, production lines, and logistics teams in real time, manufacturers can forecast demand more precisely while managing inventory more efficiently.
This leads to reduced lead times, lower inventory costs, and improved delivery performance — all of which ensures a more responsive and agile supply chain that can adapt to market changes rapidly.
Quality control
In intelligent manufacturing, quality control is enhanced through real-time monitoring and advanced analytics. On top of this, AI and machine learning algorithms analyze production data to detect anomalies and variations, enabling immediate corrective actions. Such a proactive approach ensures consistent product quality while reducing defects and minimizing the need for manual inspections.
By maintaining high quality standards, manufacturers can improve customer satisfaction while reducing costs associated with rework, returns, and waste.
Four key technologies that enable intelligent manufacturing
Unlocking the full potential of intelligent manufacturing is only possible when organizations invest in the following four technologies.
1. Real-time data platform
By collecting, processing, and analyzing data from various sources near-instantaneously, before the data loses any value, real-time data platforms enable manufacturers to make informed and intelligent decisions on the fly. Such platforms integrate data from sensors, machines, and enterprise systems to provide a comprehensive view of operations, helping to identify inefficiencies and optimize processes. By leveraging real-time insights, manufacturers can respond quickly to changes, improve operational agility, and enhance overall productivity.
2. AI/ML
Artificial intelligence and machine learning algorithms analyze vast amounts of data to uncover patterns, predict outcomes, and improve manufacturing processes. In intelligent manufacturing, AI/ML can enhance predictive maintenance, quality control, and supply chain management by providing actionable insights and automating complex decision-making. Together, these technologies enable manufacturers to improve accuracy, efficiency, and adaptability, driving continuous improvement across production.
3. IoT
By connecting devices, machines, and systems within the manufacturing environment, industrial IoT facilitates seamless data exchange and communication. IoT sensors connect real-time data on equipment performance, environmental conditions, and production metrics, providing valuable insights for monitoring and optimization. By enabling real-time visibility across the environment, IoT helps manufacturers enhance operational efficiency, reduce downtime, and improve product quality.
4. Edge computing
Edge computing infrastructure enables manufacturers to process data right where it’s generated, reducing latency and bandwidth usage by minimizing the need to transmit data to centralized servers. In intelligent manufacturing, the edge enables real-time analysis and decision-making right where production occurs, improving responsiveness and reliability. The technology also supports applications like predictive maintenance, quality control, and autonomous systems, further enhancing speed and efficiency.
Bottom line: Intelligent manufacturing requires real-time decisioning
Achieving the full promise of intelligent manufacturing is only possible when you have infrastructure that enables you to move at the speed of real time. See how Volt helps intelligent manufacturers fully capitalize on edge-IoT data.
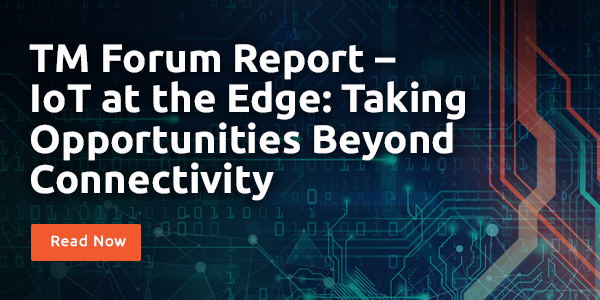